In the pharmaceutical, chemical, agrochemical and personal care industries, crystallization operations are essential. They determine the characteristics of the crystals, which are important during final operations such as filtration or drying. The main characteristics of particles are crystal shape, size and crystal size distribution (particle size distribution PSD).
Reliable information on solubility and crystallization kinetics is of utmost importance for a robust crystallization process design [1]. Commercial equipment is available to accurately measure the solubility of a solid [2]. Equipment such as the Crystal16 uses clear point measurements to determine the temperature when the suspension turns into a clear solution upon slowly heating the sample. Knowing the solubility is key information in designing crystallization processes and helps for instance in selecting the crystallization method [3].
In order to control PSD in batch crystallization, there are different proposed policies on cooling profiles, thermocycling, stirring and/or seeding. A succession of cooling and heating periods such as thermocycling has been also proposed in order to improve PSD in seeded batch cooling crystallization. The heating periods allow the dissolution of fine particles, which results in a narrow PSD. The Crystal16 and Crystalline instruments offers the possibility of performing all of these experiments in a controlled and efficient manner as early as possible during the development of an active ingredient.

Kubota and Funakoshi have already confirmed the effects of seed loading on cooling crystallization [4-6]. Moreover, they found that seeding has an impact on crystallization mechanisms such as secondary nucleation and agglomeration and on the purity of the final product. Nevertheless, there is no general rule concerning the seeding method.
Delacroix et al propose a seeding policy to control PSD for glycine crystallization based on the interaction of seed mass and seed size [7]. In batch cooling crystallization, if the seeding process is not carefully carried out, the crystal size distribution (PSD) is dispersed. The mean crystal size of the product obtained actually depends on the size of the seeds used because of the growth rate distribution.
ter Horst et al proposed recently an assessment method for secondary nucleation rates using a well-controlled, small scale seeding procedure [8]. The procedure comprises the seeding of a well-monitored, stirred, supersaturated solution by a carefully selected single crystal under conditions at which spontaneous nucleation does not occur. The conditions for the secondary nucleation measurements were established on the Crystal16 instrument by measuring the metastable zone of model compounds in the selected solvents and the induction time probability distribution for spontaneous nucleation.
Then, the secondary nucleation induced by seeding a single crystal was studied for the model compounds in supersaturated solutions using different single crystal seed sizes.The Crystalline is a multiple reactor setup in which all eight reactors can be independently controlled and monitored. The monitoring is done by the integrated cameras. The recorded images are analyzed by internal software resulting in information on the crystal size distribution such as a particle count. The determined number of particles in time were translated to a suspension density using a calibration performed with monodisperse polymer spheres. The increasing crystal suspension density in time subsequently allowed the determination of the secondary nucleation rate under very specific conditions of supersaturation and temperature.
The determination of a supersaturation threshold for secondary nucleation proposed by ter Horst et al could be used in industrial crystallization process design to identify process conditions with the right secondary nucleation rate behavior.
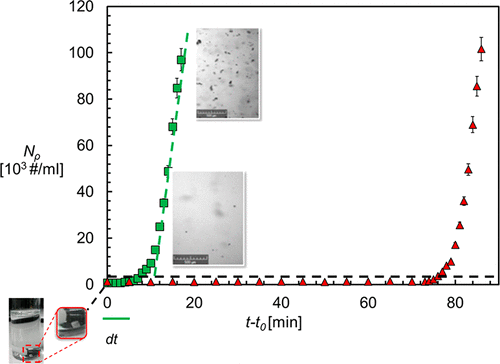
SOME DEFINITIONS
- Crystal nucleation is the formation of new small crystalline entities in a supersaturated liquid phase and, therefore, for a large part responsible for the final crystal size distribution.
- Primary crystal nucleation occurs in a clear solution in the absence of crystalline material of its own kind.
- Secondary nucleation occurs as a result of the presence of crystals of the same compound in a supersaturated suspension. Thus, in the case of secondary nucleation, parent crystals serve as a catalyst for the formation of small new crystals.
References
- J.H. ter Horst, C. Schmidt, J. Ulrich, Fundamentals of Industrial Crystallization, In: Nishinaga T, Rudolph P, editors, Handbook of Crystal Growth, Vol. II., Elsevier, 2015, pp. 1317–49.
- M.A. Reus, A.E.D.M. van der Heijden, J.H. ter Horst, Solubility Determination from Clear Points upon Solvent Addition, Org. Process Res. Dev. 19 (8) (2015) 1004–1011.
- C.J. Brown, M.L. Briuglia, J.H. ter Horst et al., Enabling Precision Manufacturing of Active Pharmaceutical Ingredients: Workflow for Seeded Cooling Continuous Crystallisations, Molecular Systems Design Engineering (2018).
- N. Kubota, D. Noihito, Powder Technol. 12 (2001) 31.
- D. Norihito, N. Kubota, A. Sato, M. Yokota, Chem. Eng. J. 81 (2001) 313.
- K. Funakoshi, H. Takiyama, M. Matsuoka, Chem. Eng. J. 81 (2001) 307.
- B. Loı¨ Mi Lung-Somarribaa, M. Moscosa-Santillanb, C. Portea, , A. Delacroix, Journal of Crystal Growth 270 (2004) 624–632
- Maria L. Briuglia, Jan Sefcik, and Joop H. ter Horst, Cryst. Growth Des. 2019, 19, 1, 421-429.
Curious to learn more?
Learn about the Crystal16 and Crystalline products for fully controlled crystallization studies.