Plastic waste from agricultural films poses environmental challenges due to its contamination and multilayered composition. Current mechanical recycling methods are limited by high contamination levels and poor quality of recyclates. To address these issues, solvent-based recycling offers a sustainable alternative by selectively recovering polymers and pigments.
In the study presented below, carried out by researchers at Ghent University, Belgium [1], Crystal16 was employed to optimize the temperature conditions for dissolution and precipitation of LDPE and EVA from agricultural films.
Experiment - Phase diagram of polymers
Agricultural films containing LDPE, EVA, and TiO2 pigments were analyzed using Crystal16 to optimize recycling conditions. Dissolution and cloud point temperatures for LDPE and EVA in xylene and limonene were measured across nine concentrations (0.1–10 wt%) within a temperature range of 3°C–95°C, under controlled stirring at 500 rpm. Five heating-cooling cycles (1°C/min) were conducted, with data from the third cycle used to refine process parameters. Figure 1 illustrates an example of dissolution temperature determination using Crystal16.
Sequential polymer recovery was achieved via cooling-induced precipitation, eliminating the need for antisolvent addition. Pigments were effectively removed through filtration. Material purities were confirmed using thermogravimetric analysis (TGA) and FTIR spectroscopy. A life cycle assessment (LCA) highlighted the process's significant environmental advantages over incineration, underscoring its sustainability.
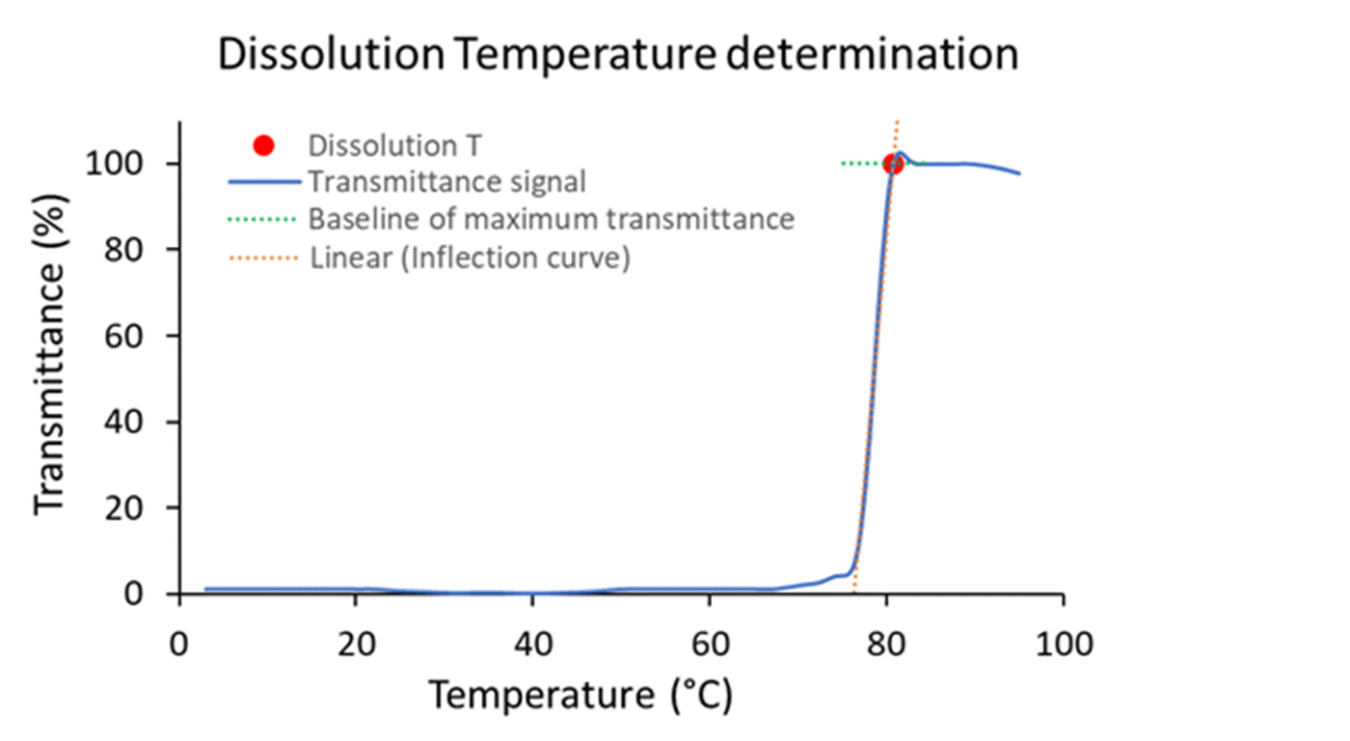
Figure 1: Example of determination of dissolution temperature for a LDPE solution in limonene 5 wt% (heating cycle).
Results
The Crystal16 experiments revealed that EVA dissolved at 45°C–63°C, while LDPE required higher temperatures of 72°C–83°C. Limonene exhibited slightly elevated dissolution temperatures compared to xylene, attributed to steric hindrance and higher viscosity. A processing temperature of 90°C was selected to ensure complete solubilization of LDPE, even at low polymer concentrations (1 wt%), ensuring broader applicability of the recycling process.
Cloud point temperatures ranged from 29°C–47°C for EVA and 58°C–71°C for LDPE, informing the selection of 40°C as the optimal temperature for LDPE precipitation. Sequential recovery of LDPE and EVA was achieved through controlled cooling, with minimal cross-contamination (≤2%). Filtration efficiently removed pigments, yielding a permeate with over 98% pure polymers.
Material purities were confirmed using thermogravimetric analysis (TGA), and the environmental impact of the process was evaluated via life cycle assessment (LCA). The LCA revealed a reduction of 3.35 kg CO2 equivalent per kg of film waste compared to incineration, highlighting the process's sustainability and environmental benefits.
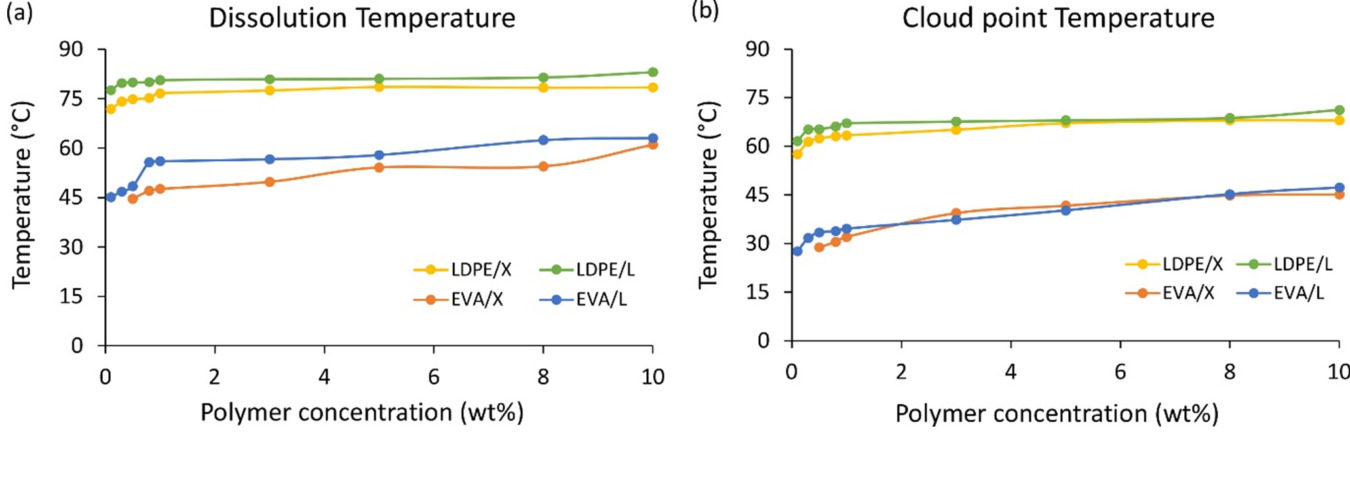
Figure 2: (a) Dissolution temperature (clear point) and (b) cloud point temperature curves for LDPE and EVA solutions in xylene (X) and limonene (L).
Conclusion
The use of Crystal16 enhanced the efficiency and precision of solvent-based recycling for agricultural films. This approach demonstrated high recovery yields and material purities, with reduced environmental impact. The findings underscore the potential of solvent-based processes, supported by advanced crystallization tools, to advance circularity in plastic recycling.
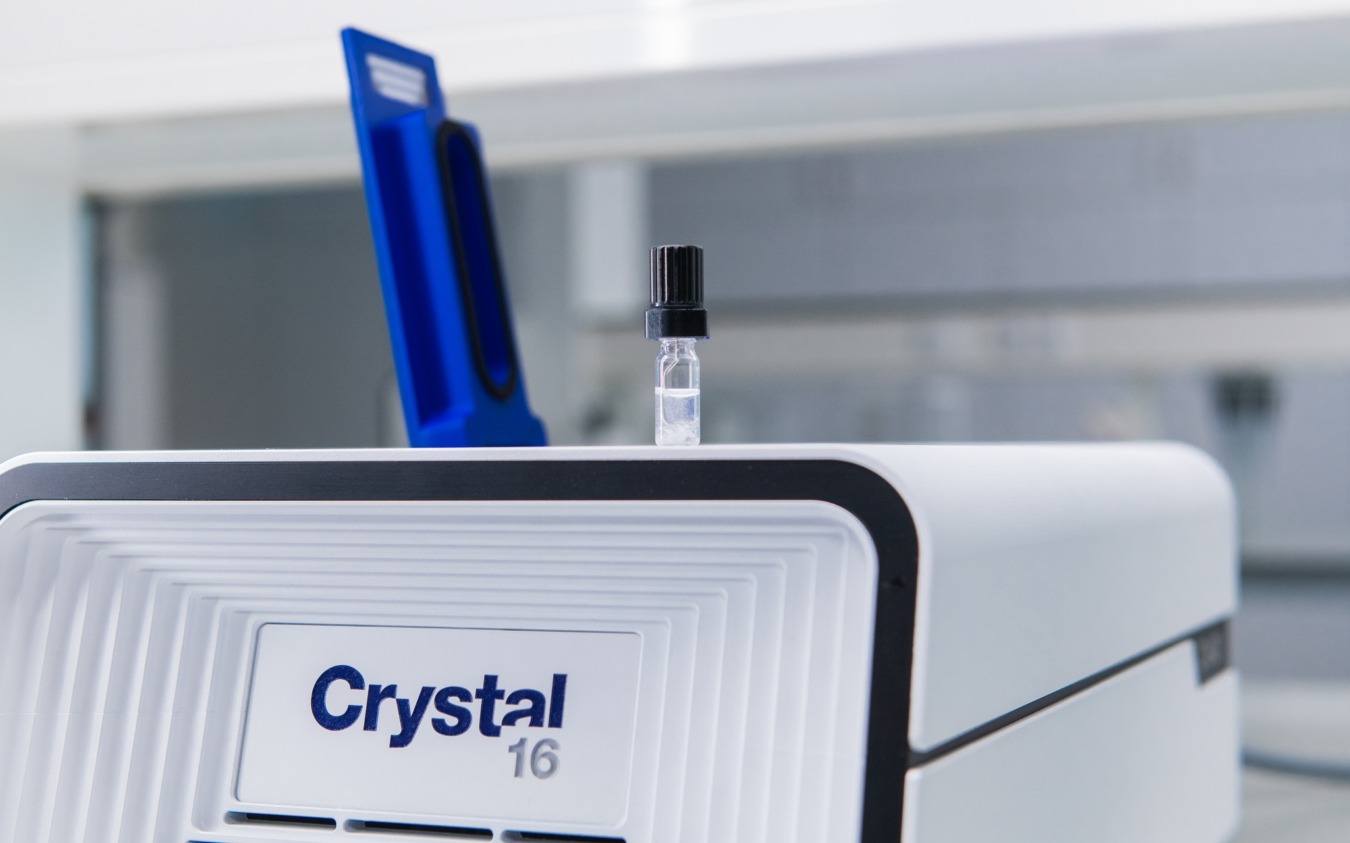
References
[1] Elisabetta Carrieri, Jordy Motte, Pieter Nachtergaele, Ine Mertens, Richard Hoogenboom, Jo Dewulf, Steven De Meester. Development of a solvent based recycling process for agricultural film, Resources, Conservation and Recycling, Volume 212, 2025, 107981, ISSN 0921-3449, https://doi.org/10.1016/j.resconrec.2024.107981